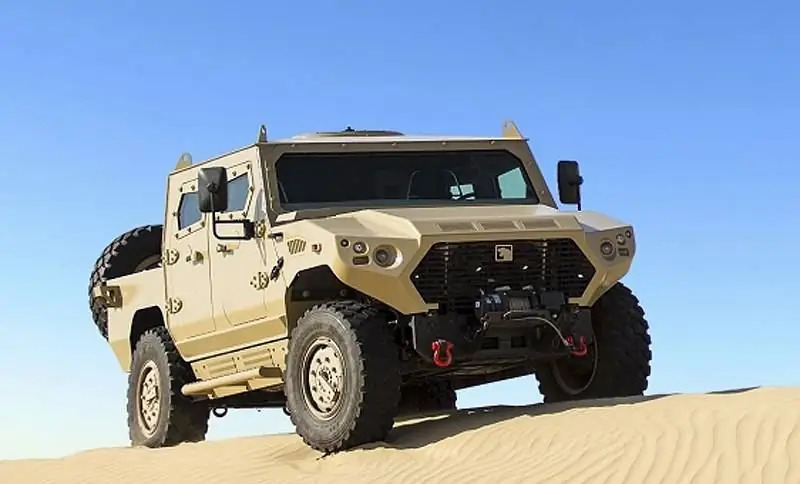
Armatura është miliona vjet më e vjetër se njerëzimi dhe është zhvilluar kryesisht për të mbrojtur kundër nofullave dhe kthetrave. Isshtë e mundur që krokodilët dhe breshkat të mund të frymëzojnë pjesërisht njerëzit për të krijuar elemente mbrojtëse. Të gjitha armët e energjisë kinetike, qoftë një klub prehistorik apo një predhë shpuese e armaturës, janë krijuar për të përqendruar forcë të madhe në një zonë të vogël, detyra e saj është të depërtojë në objektiv dhe të shkaktojë dëm maksimal mbi të. Rrjedhimisht, puna e armaturës është që ta parandalojë këtë duke devijuar ose shkatërruar mjetet sulmuese dhe / ose shpërndarë energjinë e goditjes në një zonë sa më të madhe të jetë e mundur, në mënyrë që të minimizohet çdo dëmtim i fuqisë punëtore, sistemeve të transportit dhe strukturave që mbron.
Armatura moderne zakonisht përbëhet nga një shtresë e jashtme e fortë për të ndaluar, devijuar ose shkatërruar predhën, një shtresë e ndërmjetme me një "punë për të thyer" shumë të lartë dhe një shtresë të brendshme viskoze për të parandaluar çarjet dhe mbeturinat.
Çeliku
Çeliku, i cili u bë materiali i parë i përdorur gjerësisht në krijimin e automjeteve të blinduara, është ende në kërkesë, pavarësisht shfaqjes së armaturës të bazuar në lidhjet e lehta të aluminit dhe titanit, qeramikës, kompoziteve me një polimer polimer, të përforcuar me fibra qelqi, aramidë dhe polietileni me peshë molekulare ultra të lartë, si dhe materiale të përbëra me një matricë metalike.
Shumë fabrika çeliku, përfshirë SSAB, vazhdojnë të zhvillojnë çelikë me forcë të lartë për një sërë aplikimesh kritike ndaj peshës, si veshja shtesë. Çeliku i blinduar ARM OX 600T, i disponueshëm në trashësi 4-20 mm, është i disponueshëm me një ngurtësi të garantuar prej 570 deri në 640 njësi HBW (shkurtim për Fortësinë, Brinell, Wolfram; një provë në të cilën shtypet një top tungsteni me një diametër standard në një mostër të materialit me një forcë të njohur, atëherë matet diametri i gropës së formuar; atëherë këto parametra zëvendësohen në formulën, e cila ju lejon të merrni numrin e njësive të ngurtësisë).
SSAB gjithashtu thekson rëndësinë e arritjes së ekuilibrit të duhur të fortësisë dhe fortësisë për depërtim dhe mbrojtje nga plasjet. Ashtu si të gjithë çeliqet, ARMOX 600T është i përbërë nga hekuri, karboni dhe një numër përbërësish të tjerë lidhës duke përfshirë silikon, mangan, fosfor, squfur, krom, nikel, molibden dhe bor.
Ka kufizime në teknikat e prodhimit të përdorura, veçanërisht kur bëhet fjalë për temperaturën. Ky çelik nuk është menduar për trajtim shtesë të nxehtësisë; nëse nxehet mbi 170 ° C pas dorëzimit, SSAB nuk mund të garantojë vetitë e tij. Kompanitë që mund të kapërcejnë këtë lloj kufizimi ka të ngjarë të tërheqin kontrollin e ngushtë të prodhuesve të automjeteve të blinduara.
Një kompani tjetër suedeze, Deform, ofron pjesë të forca të blinduara prej çeliku të blinduar të nxehtë të prodhuar për prodhuesit e automjeteve të blinduara, veçanërisht ata që kërkojnë të përmirësojnë mbrojtjen e automjeteve komerciale / civile.
Muret e zjarrit me një copë Deform janë instaluar në Nissan PATROL 4x4, minibus Volkswagen T6 TRANSPORTER dhe kamionçinë Isuzu D-MAX, së bashku me një fletë dysheme të ngurtë të të njëjtit material. Procesi i formimit të nxehtë të zhvilluar nga Deform dhe i përdorur në prodhimin e fletëve ruan një ngurtësi prej 600HB [HBW].
Kompania pretendon se mund të rivendosë vetitë e të gjithë çeliqeve të blinduar në treg duke ruajtur një formë të përcaktuar strukturore, ndërsa pjesët që rezultojnë janë shumë më superiore ndaj strukturave tradicionale të salduara dhe pjesërisht të mbivendosura. Në metodën e zhvilluar nga Deform, fletët shuhen dhe kaliten pas falsifikimit të nxehtë. Falë këtij procesi, është e mundur të merren forma tre-dimensionale që nuk mund të merren me formimin e ftohtë pa të detyrueshme në raste të tilla "saldime që shkelin integritetin e pikave kritike".
Fletët e çelikut të deformuara të nxehta janë përdorur në BAE Systems BVS-10 dhe CV90 dhe, që nga fillimi i viteve 1990, në shumë makina Kraus-Maffei Wegmann (KMW). Po vijnë urdhra për prodhimin e pllakave të blinduara tre-dimensionale për rezervuarin LEOPARD 2 dhe disa pllaka në formë për automjetet BOXER dhe PUMA, plus për disa automjete Rheinmetall, përfshirë përsëri BOXER, si dhe një kapak për automjetin WIESEL. Deform gjithashtu punon me materiale të tjera mbrojtëse duke përfshirë alumin, kevlar / aramid dhe titan.
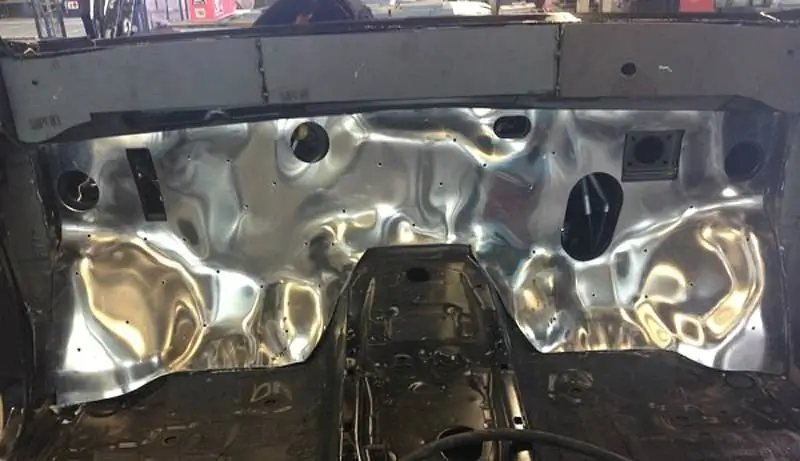
Përparimi i aluminit
Sa i përket automjeteve të blinduara, për herë të parë forca të blinduara prej alumini u përdorën gjerësisht në prodhimin e transportuesit të blinduar M113, i cili është prodhuar që nga viti 1960. Ishte një aliazh, i caktuar 5083, që përmbante 4.5% magnez dhe sasi shumë më të vogla mangani, hekuri, bakri, karboni, zinku, kromi, titani dhe të tjerë. Edhe pse 5083 ruan forcën e tij mirë pas saldimit, nuk është një aliazh i trajtueshëm me nxehtësi. Nuk ka një rezistencë aq të mirë ndaj plumbave të blinduar 7.62 mm, por, siç konfirmuan testet zyrtare, ndalon plumbat e blinduar të stilit sovjetik 14.5 mm më mirë se çeliku, duke kursyer peshë dhe duke shtuar forcën e dëshiruar. Për këtë nivel mbrojtjeje, fleta e aluminit është më e trashë dhe 9 herë më e fortë se çeliku me një densitet më të ulët prej 265 r / cm3, gjë që rezulton në një ulje të peshës së strukturës.
Prodhuesit e automjeteve të blinduara së shpejti filluan të kërkojnë forca të blinduara prej alumini më të lehta, më të forta, të saldueshme dhe të trajtueshme me nxehtësi, gjë që çoi në zhvillimin e Alcan të vitit 7039 dhe më vonë të 7017, të dyja me përmbajtje më të lartë zinku.
Ashtu si me çelikun, vulosja dhe montimi i mëvonshëm mund të ndikojnë negativisht në vetitë mbrojtëse të aluminit. Gjatë saldimit, zonat e prekura nga nxehtësia zbuten, por forca e tyre restaurohet pjesërisht për shkak të forcimit gjatë plakjes natyrore. Struktura e metalit ndryshon në zona të ngushta pranë saldimit, duke krijuar sforcime të mëdha mbetëse në rast të gabimeve të saldimit dhe / ose montimit. Rrjedhimisht, teknikat e prodhimit duhet t'i minimizojnë ato, ndërsa rreziku i plasaritjes nga korrozioni i stresit gjithashtu duhet të minimizohet, veçanërisht kur jeta e projektimit të makinës pritet të jetë më shumë se tre dekada.
Çarja e korrozionit të stresit është një proces i shfaqjes dhe rritjes së çarjeve në një mjedis gërryes, i cili tenton të përkeqësohet me rritjen e numrit të elementeve të lidhjes. Formimi i çarjeve dhe rritja e tyre e mëvonshme ndodh si rezultat i përhapjes së hidrogjenit përgjatë kufijve të kokrrës.
Përcaktimi i ndjeshmërisë ndaj plasaritjes fillon me nxjerrjen e një sasie të vogël elektroliti nga çarjet dhe analizën e tij. Testet e korrozionit të tensionit të ulët të sforcimit kryhen për të përcaktuar se sa keq është dëmtuar një aliazh i veçantë. Shtrirja mekanike e dy mostrave (njëri në një mjedis gërryes dhe tjetri në ajër të thatë) ndodh derisa ato të dështojnë, dhe pastaj të krahasohet deformimi plastik në vendin e thyerjes - sa më shumë mostra të shtrihet në dështim, aq më mirë.
Rezistenca ndaj plasaritjeve të korrozionit të stresit mund të përmirësohet gjatë përpunimit. Për shembull, sipas Total Materia, e cila e quan veten "baza e të dhënave më e madhe në botë e materialeve", Alcan ka përmirësuar performancën e 7017 në testet e përshpejtuara të plasaritjes së korrozionit të stresit me 40 herë. Rezultatet e marra gjithashtu bëjnë të mundur zhvillimin e metodave të mbrojtjes nga korrozioni për zonat e strukturave të salduara, në të cilat është e vështirë të shmangen streset e mbetura. Hulumtimet që synojnë përmirësimin e lidhjeve në mënyrë që të optimizojnë karakteristikat elektrokimike të nyjeve të salduara janë në vazhdim. Puna në lidhjet e reja të trajtueshme me nxehtësi fokusohet në përmirësimin e forcës së tyre dhe rezistencës ndaj korrozionit, ndërsa puna në lidhjet jo të trajtueshme me nxehtësi synon të heqë kufizimet e vendosura nga kërkesat për saldim. Materialet më të vështira në zhvillim do të jenë 50% më të forta se armatura më e mirë e aluminit që përdoret sot.
Lidhjet me densitet të ulët si alumini litium ofrojnë rreth 10% kursim në peshë mbi lidhjet e mëparshme me rezistencë të krahasueshme ndaj plumbave, edhe pse performanca balistike ende nuk është vlerësuar plotësisht sipas Total Materia.
Metodat e saldimit, përfshirë ato robotike, po përmirësohen gjithashtu. Ndër detyrat që zgjidhen janë minimizimi i furnizimit me nxehtësi, një hark saldimi më i qëndrueshëm për shkak të përmirësimit të sistemeve të furnizimit me energji dhe tela, si dhe monitorimi dhe kontrolli i procesit nga sistemet e ekspertëve.
MTL Advanced Materials punuan me ALCOA Defense, një prodhues i njohur i pllakave të blinduara prej alumini, për të zhvilluar atë që kompania e përshkruan si një "proces i besueshëm dhe i përsëritshëm i formimit të ftohtë". Kompania vëren se lidhjet e aluminit të zhvilluara për aplikime të blinduara nuk ishin të dizajnuara për formim të ftohtë, që do të thotë se procesi i saj i ri duhet të ndihmojë në shmangien e mënyrave të zakonshme të dështimit, përfshirë plasaritjen. Qëllimi përfundimtar është të mundësojë projektuesit e makinerive që të minimizojnë nevojën për saldim dhe të zvogëlojnë numrin e pjesëve, sipas kompanisë. Reduktimi i vëllimit të saldimit, thekson kompania, rrit forcën strukturore dhe mbrojtjen e ekuipazhit duke zvogëluar kostot e prodhimit. Duke filluar me aliazhin e vërtetuar mirë 5083-H131, kompania zhvilloi një proces për pjesët e formimit të ftohtë me një kënd përkuljeje 90 gradë përgjatë dhe përgjatë kokrrave, pastaj kaloi në materiale më komplekse, për shembull, lidhjet 7017, 7020 dhe 7085, gjithashtu duke arritur rezultate të mira.
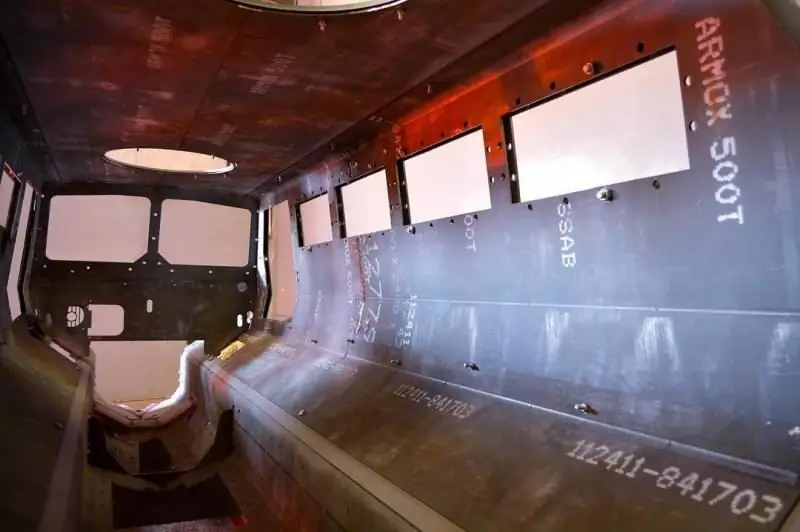
Qeramikë dhe përbërje
Disa vjet më parë, Morgan Advanced Materials njoftoi zhvillimin e disa sistemeve të blinduara SAMAS, të cilat përbëheshin nga një kombinim i qeramikës së avancuar dhe përbërjeve strukturore. Linja e produktit përfshin forca të blinduara të varura, veshje kundër fragmentimit, kapsula të mbijetesës të bëra nga përbërje strukturore për zëvendësimin e trupave metalikë dhe mbrojtjen e moduleve të armëve, të banuara dhe të pabanuara. Të gjithë ata mund të përshtaten me kërkesat specifike ose të bëhen me porosi.
Ofron mbrojtje STANAG 4569 Niveli 2-6, së bashku me performancën me shumë ndikime dhe kursimin e peshës (kompania pretendon se këto sisteme peshojnë gjysmën e produkteve të ngjashme të çelikut) dhe përshtaten me kërcënimet, platformat dhe misionet specifike. … Veshjet kundër copëzimit mund të bëhen nga panele të sheshta që peshojnë 12.3 kg për të mbuluar një sipërfaqe prej 0.36 m2 (rreth 34 kg / m2) ose pajisje të ngurta që peshojnë 12.8 kg për 0.55 m2 (rreth 23.2 kg / m2).
Sipas Morgan Advanced Materials, forca të blinduara shtesë të krijuara për të reja dhe modernizimin e platformave ekzistuese ofrojnë të njëjtat aftësi në gjysmën e peshës. Sistemi i patentuar siguron mbrojtje maksimale kundër një game të gjerë kërcënimesh, duke përfshirë armë të kalibrit të vogël dhe të mesëm, pajisje shpërthyese të improvizuara (IED) dhe granata me raketa, si dhe performancë me shumë ndikime.
Një sistem i blinduar "gjysmë strukturor" me rezistencë të mirë ndaj korrozionit ofrohet për modulet e armëve (përveç aplikimeve të ajrit dhe detit), dhe së bashku me kursimin e peshës dhe minimizimin e problemeve me qendrën e gravitetit, ndryshe nga çeliku, krijon më pak probleme të përputhshmërisë elektromagnetike Me
Mbrojtja e moduleve të armëve është një problem i veçantë, pasi ato janë një objektiv tërheqës, pasi paaftësia e tyre dëmton në mënyrë drastike komandën e ekuipazhit të situatës dhe aftësinë e automjetit për t'u përballur me kërcënimet aty pranë. Ata gjithashtu kanë optoelektronikë delikate dhe motorë elektrikë të prekshëm. Meqenëse ato zakonisht instalohen në krye të automjetit, armatimi duhet të jetë i lehtë në mënyrë që të mbajë qendrën e gravitetit sa më të ulët të jetë e mundur.
Sistemi i mbrojtjes së moduleve të armëve, i cili mund të përfshijë xham të blinduar dhe mbrojtje të pjesës së sipërme, është plotësisht i palosshëm, dy persona mund ta montojnë përsëri në 90 sekonda. Kapsulat e përbëra të mbijetesës janë bërë nga ajo që kompania i përshkruan si "materiale unike të forta dhe formulime polimerësh", ato ofrojnë mbrojtje nga copëzat dhe mund të riparohen në terren.
Mbrojtja e ushtarit
SPS (Sistemi i Mbrojtjes së Ushtarëve) i zhvilluar nga 3M Ceradyne përfshin helmeta dhe futje në forca të blinduara të trupit për Sistemin e Integruar të Mbrojtjes së Kokës (IHPS) dhe VTP (Vital Torso Protection) - përbërësit ESAPI (Enhanced Small Arms Protective Insert) - futje e përmirësuar për mbrojtje kundër armë të vogla) të sistemit SPS.
Kërkesat e IHPS përfshijnë peshë më të lehtë, mbrojtje pasive të dëgjimit dhe mbrojtje të përmirësuar të goditjes. Sistemi gjithashtu përfshin pajisje të tilla si një komponent për të mbrojtur nofullën e poshtme të një ushtari, një maskë mbrojtëse, një montim për syzet e shikimit të natës, udhëzues për, për shembull, elektrik dore dhe kamerë, dhe mbrojtje shtesë modulare nga plumbat. Kontrata, me vlerë më shumë se 7 milion dollarë, parashikon furnizimin e rreth 5,300 helmetave. Ndërkohë, më shumë se 30,000 komplete ESAPI - futje më të lehta për forca të blinduara të trupit - do të dorëzohen sipas kontratës prej 36 milion dollarësh. Prodhimi i të dy këtyre kompleteve filloi në 2017.
Gjithashtu nën programin SPS, KDH Defense zgjodhi materialet e Honeywell's SPECTRA SHIELD dhe GOLD SHIELD për pesë nënsisteme, përfshirë nënsistemin Torso and Extremity Protection (TEP) që do të furnizohet për projektin SPS. Sistemi i mbrojtjes TEP është 26% më i lehtë, gjë që përfundimisht zvogëlon peshën e sistemit SPS me 10%. KDH do të përdorë SPECTRA SHIELD, e cila bazohet në fibrat UHMWPE, dhe GOLD SHIELD, bazuar në fibrat aramid, në produktet e veta për këtë sistem.
Fibër SPECTRA
Honeywell përdor një proces të tjerrjes dhe vizatimit të fibrave polimer të pronarit për të futur lëndën e parë UHMWPE në fibër SPECTRA. Ky material është 10 herë më i fortë se çeliku për sa i përket peshës, forca e tij specifike është 40% më e lartë se ajo e fibrave aramide, ka një pikë shkrirjeje më të lartë se polietileni standard (150 ° C) dhe rezistencë më të madhe ndaj konsumit në krahasim me polimeret e tjerë, për shembull, poliestër.
Materiali i fortë dhe i ngurtë SPECTRA tregon deformim të lartë në thyerje, domethënë shtrihet shumë fort para thyerjes; kjo veti lejon të absorbohet një sasi e madhe e energjisë së ndikimit. Honeywell pohon se përbërjet e fibrave SPECTRA performojnë shumë mirë nën ndikimet e shpejtësisë së lartë, siç janë plumbat e pushkëve dhe valët e goditjes. Sipas kompanisë, "Fibra jonë e avancuar reagon ndaj ndikimit duke hequr shpejt energjinë kinetike nga zona e goditjes … gjithashtu ka amortizim të mirë të dridhjeve, rezistencë të mirë ndaj deformimeve të përsëritura dhe karakteristika të shkëlqyera të fërkimit të brendshëm të fibrave së bashku me rezistencë të shkëlqyer ndaj kimikateve, uji dhe drita UV ".
Në teknologjinë e tij SHIELD, Honeywell përhap fijet paralele të fibrave dhe i lidh ato së bashku duke i mbarsur me një rrëshirë të avancuar për të krijuar një fjongo njëdrejtimëshe. Pastaj shtresat e kësaj kasete vendosen në mënyrë tërthore në këndet e dëshiruara dhe në një temperaturë dhe presion të caktuar, ngjitur në një strukturë të përbërë. Për aplikime të buta të veshshme, ajo është e petëzuar midis dy shtresave të filmit transparent të hollë dhe fleksibël. Për shkak se fijet mbeten të drejta dhe paralele, ato shpërndajnë energjinë e ndikimit në mënyrë më efikase sesa nëse do të ishin të endura në një pëlhurë të endur.
Short Bark Industries gjithashtu përdor SPECTRA SHIELD në truprojën BCS (Ballistic Combat Shirt) për sistemin SPS TEP. Short Bark specializohet në mbrojtje të butë, veshje taktike dhe pajisje shtesë.
Sipas Honeywell, ushtarët zgjodhën elementë mbrojtës të bërë nga këto materiale pasi ata demonstruan performancë superiore mbi homologët e tyre të fibrave aramide.